Postage Lockers
Postage Lockers: Modern package delivery has transformed dramatically over the past decade. Additionally, the rise of e-commerce has created unprecedented demand for secure delivery solutions. Furthermore, consumers increasingly expect convenient collection options that fit their busy lifestyles. Consequently, postage lockers have emerged as the ideal solution for safe and efficient package handling.
The growth in online shopping continues to accelerate year on year. Moreover, traditional delivery methods often struggle to meet customer expectations. Subsequently, missed deliveries cost both retailers and consumers time and money. Therefore, innovative solutions like automated collection systems have become essential infrastructure for modern communities.
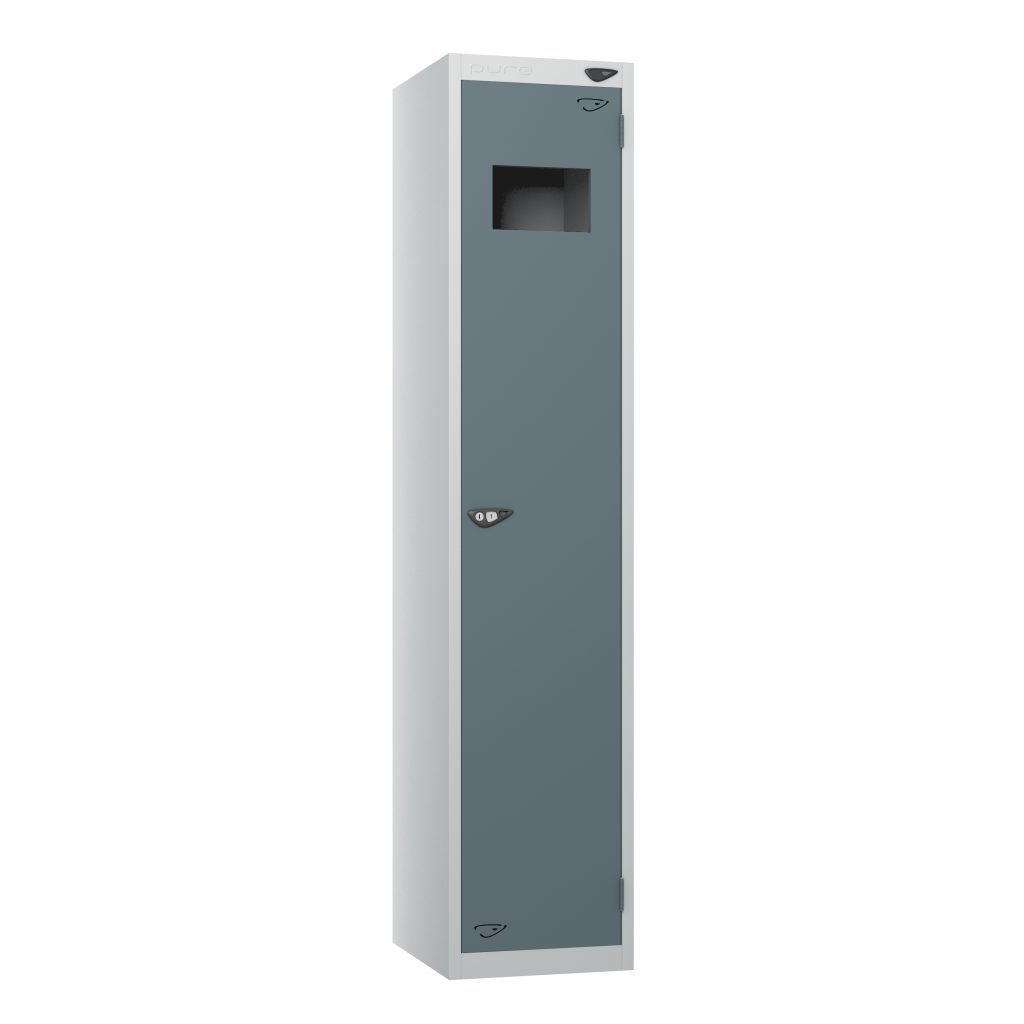
Understanding Postage Lockers and Their Revolutionary Impact
Postage lockers represent cutting-edge technology in package delivery management. Additionally, these automated systems provide secure storage for parcels of various sizes. Furthermore, they operate around the clock, offering unparalleled convenience for busy recipients. Consequently, both retailers and customers benefit from improved delivery success rates.
The technology behind automated parcel systems continues to evolve rapidly. Moreover, modern units incorporate advanced security features and user-friendly interfaces. Subsequently, recipients can collect their packages at any time using simple authentication methods. Therefore, these systems eliminate the frustration of missed deliveries whilst enhancing customer satisfaction.
Security remains paramount in package locker design and operation. Additionally, multiple authentication methods ensure only authorised recipients access their parcels. Furthermore, robust construction protects valuable contents from theft and weather damage. Consequently, retailers can offer premium delivery services with complete confidence in package security.
Benefits of Implementing Postage Lockers in Communities
Package delivery efficiency improves dramatically with automated locker systems. Moreover, delivery drivers can complete multiple deliveries to a single location quickly. Subsequently, this efficiency reduces delivery costs whilst improving service reliability. Additionally, recipients enjoy flexible collection times that suit their schedules perfectly.
Environmental benefits also emerge from centralised delivery systems. Furthermore, reduced delivery attempts lower carbon emissions from delivery vehicles. Moreover, consolidated deliveries minimise packaging waste and transportation impact. Therefore, communities can enhance sustainability whilst improving delivery services.
Customer satisfaction increases significantly with convenient collection options. Additionally, secure storage eliminates concerns about package theft or damage. Furthermore, extended collection hours accommodate various work schedules and lifestyle preferences. Consequently, retailers often report improved customer loyalty and repeat purchases.
Types of Postage Lockers Available in Today’s Market
Commercial grade systems offer robust solutions for high-volume locations. Moreover, these units feature heavy-duty construction and advanced management software. Subsequently, they handle hundreds of deliveries daily whilst maintaining optimal performance. Additionally, enterprise-level systems integrate seamlessly with existing logistics networks.
Residential scale units provide perfect solutions for apartment complexes and housing developments. Furthermore, these systems offer secure package storage for multiple residents simultaneously. Moreover, they eliminate the need for individual doorstep deliveries in multi-unit buildings. Therefore, property managers can enhance resident satisfaction whilst improving security.
Indoor Postage Lockers for Protected Environments
Indoor installations provide maximum protection from weather and environmental factors. Additionally, climate-controlled environments preserve sensitive packages and electronics. Furthermore, indoor locations often offer enhanced security through building access controls. Consequently, premium retailers frequently specify indoor installations for valuable merchandise.
Lobby installations prove particularly popular in office buildings and residential towers. Moreover, these locations provide convenient access whilst maintaining building security protocols. Subsequently, residents and workers can collect packages during regular building hours. Therefore, indoor systems often achieve higher utilisation rates than outdoor alternatives.
Mall and shopping centre installations capture high foot traffic effectively. Additionally, these locations offer extended hours and climate-controlled environments. Furthermore, retailers can position collection points near their physical stores strategically. Consequently, collection visits often generate additional shopping opportunities and sales.
Outdoor Postage Lockers for Maximum Accessibility
Weather-resistant outdoor units provide round-the-clock accessibility regardless of conditions. Moreover, these systems feature robust construction designed to withstand harsh weather. Subsequently, recipients can collect packages at any hour without building access restrictions. Additionally, outdoor installations often serve larger geographical areas effectively.
Parking lot installations offer exceptional convenience for drive-up collection. Furthermore, these locations provide easy vehicle access for large package retrieval. Moreover, adequate lighting and security features ensure safe collection experiences. Therefore, retail parks and shopping centres frequently choose parking lot installations.
Streetside installations bring package collection directly to residential neighbourhoods. Additionally, these locations reduce travel time for recipients significantly. Furthermore, strategic placement can serve multiple streets and housing areas efficiently. Consequently, local authorities often support streetside installations to improve community services.
Comprehensive Guide to Postage Lockers Sizes and Configurations
Package size diversity demands flexible locker configurations to accommodate various delivery requirements. Moreover, modern systems offer multiple compartment sizes within single installations. Subsequently, retailers can store everything from small electronics to large household items. Additionally, adjustable compartments provide maximum flexibility for changing package sizes.
Standardised sizing ensures compatibility with major carrier delivery requirements. Furthermore, industry-standard dimensions accommodate common package formats efficiently. Moreover, predictable sizing helps customers understand collection options before making purchases. Therefore, standardised configurations support seamless integration with existing delivery networks.
Small Compartment Postage Lockers for Compact Deliveries
Compact compartments handle the majority of online purchases effectively. Additionally, these spaces accommodate electronics, clothing, and small household items perfectly. Furthermore, efficient use of small spaces maximises the number of available storage units. Consequently, high-traffic locations can serve more customers within limited installation areas.
Document and small package storage meets essential business and personal needs. Moreover, these compartments provide secure storage for valuable documents and contracts. Subsequently, legal firms and businesses often rely on these services for confidential deliveries. Therefore, professional services frequently specify enhanced security features for small compartment systems.
Pharmaceutical and medical supplies require secure storage with controlled access. Additionally, temperature monitoring ensures medication integrity during storage periods. Furthermore, audit trails track access for regulatory compliance requirements. Consequently, healthcare providers increasingly adopt specialised locker systems for sensitive deliveries.
Medium Compartment Postage Lockers for Standard Packages
Standard retail packages fit comfortably in medium-sized compartments. Moreover, these spaces accommodate typical online shopping deliveries efficiently. Subsequently, fashion retailers and general merchandise companies rely heavily on medium compartments. Additionally, these sizes handle gift packages and seasonal deliveries effectively.
Electronics and technology products often require medium compartment storage. Furthermore, protective packaging for fragile items demands adequate space allowances. Moreover, customer expectations for undamaged electronics make proper sizing crucial. Therefore, technology retailers frequently specify medium compartments for optimal product protection.
Home improvement and DIY supplies benefit from medium compartment accessibility. Additionally, tools and hardware items often require secure storage before collection. Furthermore, weekend collection patterns suit DIY enthusiasts’ shopping habits perfectly. Consequently, home improvement retailers report excellent customer satisfaction with medium compartment systems.
Large Compartment Postage Lockers for Oversized Items
Appliance and furniture deliveries require spacious storage solutions. Moreover, these compartments accommodate items that exceed standard shipping dimensions. Subsequently, customers can purchase larger items with confidence in secure delivery. Additionally, large compartments often feature enhanced access mechanisms for heavy items.
Bulk grocery and household supply deliveries utilise large compartments effectively. Furthermore, family shopping orders often exceed standard package sizes significantly. Moreover, cost-effective bulk purchasing becomes viable with adequate storage space. Therefore, grocery retailers increasingly offer large compartment collection services.
Seasonal and holiday deliveries peak during specific periods throughout the year. Additionally, gift packages and decorations often require oversized storage space. Furthermore, holiday shopping patterns create temporary demand spikes for large compartments. Consequently, flexible sizing helps accommodate seasonal delivery variations efficiently.
Colour Options and Customisation for Postage Lockers
Corporate branding opportunities transform functional lockers into marketing assets. Moreover, custom colours and graphics enhance brand visibility in high-traffic areas. Subsequently, retailers can extend their brand presence beyond traditional store locations. Additionally, consistent branding creates professional appearances that build customer trust.
Community integration becomes seamless with thoughtful colour selection and design. Furthermore, neutral colours blend harmoniously with existing architectural elements. Moreover, local councils often specify colour requirements to maintain aesthetic standards. Therefore, flexible colour options ensure compliance with planning and design guidelines.
Standard Colour Schemes for Postage Lockers
Professional colour palettes enhance corporate image and customer confidence. Additionally, classic combinations like grey and blue convey reliability and trustworthiness. Furthermore, these colours require minimal maintenance whilst providing lasting visual appeal. Consequently, many businesses choose standard schemes for cost-effective professional appearance.
High-visibility colours improve safety and accessibility in various lighting conditions. Moreover, bright colours help customers locate collection points quickly and easily. Subsequently, emergency services can identify locations rapidly when required. Therefore, safety considerations often influence colour selection decisions significantly.
Weather-resistant finishes ensure long-lasting colour retention despite environmental exposure. Additionally, fade-resistant coatings maintain professional appearance throughout extended service life. Furthermore, easy-clean surfaces reduce maintenance requirements and operational costs. Consequently, durable finishes provide excellent long-term value for installation investments.
Custom Colour Solutions for Postage Lockers
Brand-specific colours strengthen corporate identity and customer recognition. Moreover, custom colours can incorporate exact corporate colour specifications accurately. Subsequently, installations become extension of existing brand environments seamlessly. Additionally, colour consistency across multiple locations reinforces brand presence effectively.
Architectural integration requires careful colour coordination with surrounding environments. Furthermore, custom colours can complement existing building schemes perfectly. Moreover, planning authorities often approve installations more readily with sympathetic colour choices. Therefore, architectural consultation during colour selection proves valuable for project success.
Seasonal colour variations create dynamic installations that engage community interest. Additionally, changeable panels allow periodic updates without complete system replacement. Furthermore, holiday themes and local events can influence temporary colour schemes. Consequently, flexible colour systems maintain community engagement throughout the year.
Lead Times and Planning for Postage Lockers Installation
Project planning requires comprehensive understanding of lead times and delivery schedules. Additionally, custom specifications and high-demand periods can extend delivery timeframes. Furthermore, early planning ensures project completion within desired timeframes. Consequently, successful installations depend on realistic scheduling and proactive planning.
Supply chain factors significantly influence delivery schedules for locker systems. Moreover, global shipping and component availability affect manufacturing timelines. Subsequently, early ordering helps secure preferred delivery dates. Therefore, project managers should anticipate potential delays and plan accordingly.
Standard Lead Times for Postage Lockers
Stock configurations typically ship within two to four weeks from order confirmation. Moreover, standard colours and sizes benefit from maintained inventory levels. Subsequently, urgent installations can often proceed quickly with standard specifications. Additionally, express shipping options may further reduce delivery times when required.
Volume orders may require extended manufacturing periods despite standard specifications. Furthermore, large installations often involve custom site preparation requirements. Moreover, coordination with multiple stakeholders can extend overall project timelines. Therefore, bulk orders require careful scheduling and stakeholder management.
Seasonal demand patterns affect availability during peak installation periods. Additionally, autumn installations often prepare for increased holiday delivery volumes. Furthermore, spring installations align with new development completions. Consequently, early booking secures preferred installation dates during busy periods.
Factors Affecting Postage Lockers Lead Times
Custom specifications require additional manufacturing time and specialised processes. Moreover, bespoke colours and branding elements extend standard production schedules. Subsequently, unique requirements may add several weeks to delivery timelines. Therefore, custom installations require extended planning periods for successful completion.
Site preparation requirements can significantly impact overall project schedules. Additionally, electrical and network infrastructure must be completed before installation. Furthermore, planning permissions and local authority approvals may cause delays. Consequently, comprehensive site surveys help identify potential scheduling challenges early.
Integration requirements with existing systems may extend commissioning periods. Moreover, software configuration and testing require additional time allowances. Subsequently, complex integrations benefit from extended commissioning schedules. Therefore, system integration planning should begin during early project phases.
Installation and Setup Procedures
Professional installation ensures optimal system performance and longevity. Additionally, experienced technicians understand local requirements and regulations completely. Furthermore, proper installation minimises future maintenance requirements and operational issues. Consequently, professional installation often proves cost-effective despite initial expense.
Site preparation requires careful planning and coordination with multiple trades. Moreover, electrical supply and network connectivity must be established before installation. Subsequently, proper foundations and security measures ensure long-term system stability. Therefore, comprehensive site preparation prevents costly delays and modifications.
Pre-Installation Requirements
Electrical supply specifications must meet system requirements for reliable operation. Additionally, backup power systems ensure continued operation during power outages. Furthermore, proper earthing and surge protection safeguard electronic components. Consequently, electrical installation should comply with relevant safety standards.
Network connectivity enables remote monitoring and management capabilities. Moreover, reliable internet connection supports software updates and troubleshooting. Subsequently, backup connectivity options provide redundancy for critical installations. Therefore, network planning should consider future expansion and upgrade requirements.
Physical security measures protect installations from vandalism and unauthorised access. Additionally, lighting and CCTV systems enhance safety for users. Furthermore, proper anchoring prevents theft of entire units. Consequently, security planning should address both system and user protection requirements.
Professional Installation Services
Certified technicians ensure compliance with manufacturer specifications and local regulations. Moreover, professional installation includes comprehensive testing and commissioning procedures. Subsequently, warranty coverage often requires professional installation for validity. Therefore, certified installation protects both performance and warranty coverage.
Training programmes help facility staff understand operation and basic maintenance procedures. Additionally, comprehensive documentation supports ongoing system management. Furthermore, emergency contact procedures ensure rapid response to technical issues. Consequently, proper training maximises system uptime and user satisfaction.
Post-installation support includes monitoring services and preventive maintenance programmes. Moreover, remote diagnostics identify potential issues before they affect service. Subsequently, proactive maintenance prevents costly emergency repairs and downtime. Therefore, comprehensive support agreements provide excellent long-term value.
Technology Integration and Smart Features
Advanced software platforms provide comprehensive management and reporting capabilities. Additionally, real-time monitoring ensures optimal system performance and availability. Furthermore, automated alerts notify managers of maintenance requirements and issues. Consequently, smart management systems maximise uptime whilst minimising operational costs.
Mobile applications enhance user experience through convenient package notifications and collection instructions. Moreover, smartphone integration provides seamless access without additional hardware requirements. Subsequently, customers can receive instant notifications when packages arrive. Therefore, mobile technology significantly improves customer satisfaction and system utilisation.
Remote Management Capabilities
Cloud-based platforms enable management from any location with internet access. Additionally, multiple site management becomes efficient through centralised control systems. Furthermore, performance analytics help optimise operations and identify improvement opportunities. Consequently, remote management reduces operational costs whilst improving service quality.
Predictive maintenance systems identify potential issues before they cause service interruptions. Moreover, component monitoring extends system lifespan through proactive replacement schedules. Subsequently, planned maintenance reduces emergency repair costs and downtime. Therefore, intelligent monitoring provides excellent return on investment.
Usage analytics provide valuable insights into customer behaviour and system performance. Additionally, peak usage patterns help optimise staffing and maintenance schedules. Furthermore, capacity planning benefits from detailed utilisation data. Consequently, data-driven management improves both efficiency and customer satisfaction.
Security and Access Control
Multi-factor authentication ensures only authorised recipients access their packages. Moreover, biometric options provide enhanced security for high-value deliveries. Subsequently, audit trails track all access events for security and compliance purposes. Therefore, advanced authentication protects both packages and system integrity.
Encryption technology protects sensitive customer data and transaction information. Additionally, secure communication protocols prevent unauthorised access to system controls. Furthermore, regular security updates maintain protection against evolving threats. Consequently, robust security measures build customer trust and confidence.
Emergency access procedures ensure package retrieval during system malfunctions. Moreover, manual override capabilities prevent customer inconvenience during technical issues. Subsequently, backup access methods maintain service continuity despite component failures. Therefore, comprehensive contingency planning ensures reliable service delivery.
Maintenance and Operational Considerations
Preventive maintenance schedules ensure optimal system performance throughout operational life. Additionally, regular inspections identify wear patterns and potential issues early. Furthermore, component replacement schedules prevent unexpected failures and service interruptions. Consequently, systematic maintenance reduces total cost of ownership significantly.
Cleaning protocols maintain professional appearance and hygienic conditions. Moreover, regular cleaning prevents buildup of dirt and debris that could affect operation. Subsequently, clean installations create positive impressions and encourage continued usage. Therefore, appearance maintenance supports both functionality and customer satisfaction.
Daily Operational Procedures
System monitoring ensures all compartments function correctly and remain available for use. Additionally, daily checks identify any damaged or malfunctioning components quickly. Furthermore, prompt attention to minor issues prevents escalation into major problems. Consequently, regular monitoring maximises system availability and reliability.
Customer support procedures address collection issues and system queries efficiently. Moreover, clear escalation processes ensure rapid resolution of complex problems. Subsequently, excellent customer service maintains high satisfaction levels and continued usage. Therefore, comprehensive support procedures protect customer relationships and system reputation.
Security monitoring ensures installations remain secure and protected from tampering. Additionally, surveillance systems deter vandalism and provide evidence if incidents occur. Furthermore, regular security assessments identify vulnerabilities and improvement opportunities. Consequently, ongoing security vigilance protects both systems and users effectively.
Long-Term System Care
Component replacement schedules ensure continued reliable operation as systems age. Moreover, planned replacements prove more cost-effective than emergency repairs. Subsequently, inventory management ensures spare parts availability when needed. Therefore, proactive replacement strategies minimise downtime and operational disruption.
Software updates maintain security and functionality whilst adding new features. Additionally, regular updates ensure compatibility with evolving delivery networks and requirements. Furthermore, updated systems often provide improved performance and user experience. Consequently, systematic update management protects investment value and system relevance.
Performance optimisation ensures systems continue meeting operational requirements efficiently. Moreover, regular tuning maximises throughput and minimises energy consumption. Subsequently, optimised systems provide better return on investment throughout their service life. Therefore, ongoing optimisation maintains competitive advantage and cost-effectiveness.
Conclusion: Maximising Benefits from Modern Package Solutions
Strategic implementation of automated parcel systems transforms package delivery efficiency and customer satisfaction. Moreover, proper planning and professional installation ensure optimal performance from day one. Subsequently, facilities can enhance their service offerings whilst reducing operational costs. Additionally, modern systems provide scalable solutions that grow with changing requirements.
Success with package locker systems requires comprehensive planning, quality equipment, and ongoing support. Furthermore, integration with existing operations enhances overall efficiency and customer experience. Moreover, proper maintenance ensures reliable service throughout extended operational periods. Therefore, investment in professional systems delivers lasting benefits for both operators and customers.
Forward-thinking organisations recognise automated package systems as essential infrastructure for modern commerce. Additionally, these systems support business growth whilst improving customer satisfaction and retention. Furthermore, sustainable delivery solutions align with environmental responsibilities and community expectations. Consequently, investing in professional package locker systems becomes a strategic decision that delivers competitive advantage and operational excellence.
Companies like Total Locker Service demonstrate the importance of partnering with experienced suppliers who understand the complexities of modern package delivery requirements. Therefore, working with established providers ensures access to quality products, professional installation, and comprehensive ongoing support throughout the system lifecycle.